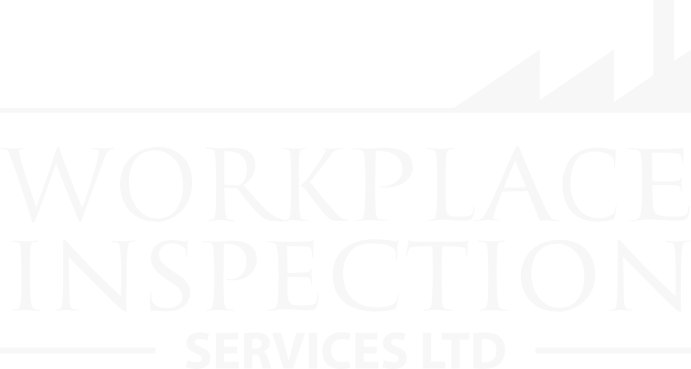
Businesses that expose employees to hazardous substances are required to use safety equipment such as a dust extraction system or fume extraction system to provide a safe and healthy working environment.
The process of COSHH LEV testing involves experts carrying out a thorough examination of the equipment to check that it’s operating efficiently. By law, this must be carried out by a competent person who has the appropriate knowledge and skills to identify and resolve any problems within the system.
Specialist LEV testing equipment is used to assess the system’s performance, design and maintenance. It commonly involves measuring the pressure drops, airflow rates and the filtration systems’ effectiveness. The condition of the filters, ducting and fans is examined to make sure they’re in full working order.
It is a legal requirement in the UK to carry out LEV testing, with the frequency depending on the types of substances being used and the associated levels of risk.
Stage 1: A thorough visual and structural examination
This is stage is to verify that the LEV is in efficient working order, in good repair and in a clean condition and may include a thorough external examination of all parts of the system, looking for damage, wear and tear, internal duct examinations, examination of any filter cleaning devices work correctly, inspection of the filter fabric and where filters have built-in pressure gauges, checks on their function and that the operating pressure is correct, checks of the water flow and sump condition in a wet scrubber, checks that the monitors and alerts/alarms are functioning correctly, inspection of the air mover drive mechanism, checks for indications of effectiveness.
Stage 2: A review of technical performance
This stage checks the conformity with commissioning or other sources of relevant information and may include observations, challenge testing, dust lamp testing, measurements, additional checks to individual components and calculations of volume flow rates.
Stage 3: Assessment of control effectiveness
The stage is to ensure that the LEV can continue to perform as intended by design and will contribute to the adequate control of exposure and includes a visual and structural examination, observations of the process and contaminant sources and he way in which operators use the LEV, challenge tests, appropriate measurements and a comparison of measurements made with any employer records of air sampling relevant to LEV performance and information on the way operators use the LEV.
You should have your LEV system tested regularly for several reasons. Very importantly, it ensures the system is providing the best protection for your workforce. This reduces the risk of health issues caused by hazardous substances in the workplace such as respiratory problems, cancer and skin irritation.
In addition, thorough testing on a regular basis can identify any system problems before they become more serious, preventing potentially expensive repairs and the associated downtime: it can help keep the system fully functional over a longer period of time.
Regular testing helps your business to comply with COSHH regulations. Failure to do so may not only result in employees falling ill, but it can also lead to fines, legal action and serious damage to your company’s reputation.
There are an estimated 19,000 new cases of breathing and lung problems annually in the UK, when sufferers have cited their workplace as causing or worsening their condition; occupational lung disease leads to the deaths of 12,000 people every year.
The penalties for companies who fail to protect employees from exposure to hazardous substances are severe. In 2023, a woodworking company was fined £25,000 for failing to control employee exposure to wood dust. The case followed an inspection of the company by the HSE in 2019, which identified there were failings in the control measures.
A second case saw a furniture company fined £16,000 after failing to protect the workforce from exposure to wood dust. At the time, the HSE reiterated how vital it was for companies to carry out statutory thorough inspections of extraction equipment, as demanded by COSHH, to prevent the ill health of employees.
In conclusion, COSHH LEV testing plays a crucial role in managing the risks to employees who are working with hazardous substances. It will also identify any potential issues with your system before they worsen, ensuring compliance with the COSHH workplace safety laws.
Yes, the Control of Substances Hazardous to Health (2002) is a legal requirement for compliance with health and safety standards.
LEV (Local Exhaust Ventilation) systems should be inspected and tested at regular intervals to ensure they remain effective. A common recommendation is to have LEV systems inspected at least once every 14 months.
LEV inspections should be carried out by a competent person or a specialist LEV testing service. Sch
Individuals should be compliant at P601.
For expert inspections, visit our Request a Quote page, and we’ll provide a tailored quote for your needs!