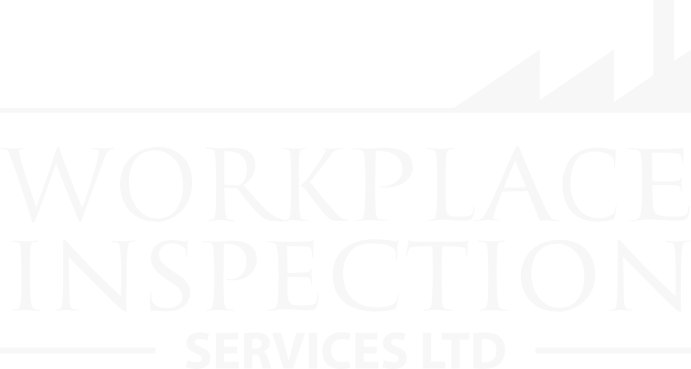
The purpose of an inspection is to identify whether work equipment can be operated, adjusted and maintained safely, with any deterioration detected and remedied before it results in a health and safety risk.
Inspection is necessary for any equipment where significant risks to health and safety may arise from incorrect installation, reinstallation, deterioration or any other circumstances.
The result of the inspection should be recorded and this record should be kept at least until the next inspection of that equipment. These should be held securely and made available upon request by any enforcing authority.
Work equipment that requires inspection should not be used, unless you know the inspection has taken place. It should be accompanied by physical evidence in the way of an inspection report.
An additional service can also be provided in way of labelling or tagging. Find out more via our Supplementary Testing.
The need for inspection and inspection frequencies should be determined through risk assessment. Find out more via our Plant Industry Guide.
For expert inspections, visit our Request a Quote page, and we’ll provide a tailored quote for your needs!
Statutory inspections are mandatory examinations or assessments required by law or regulations to ensure compliance with specific standards or safety requirements.
Non-statutory inspections are completed on all types of work equipment that do not come under a specific standard or have a legal requirement. Equipment is examined to ensure it’s integrity under Health & Safety.
These are vital for creating a safe working environment for your employees and complying with health and safety legislation.
Unsafe operating practices can often lead to accidents which may result in injuries to your employees or the public. This can lead to costly liability claims often resulting in criminal prosecutions for companies or individuals.
The HSE’s approved codes of practice and industry standards and manufacturers’ recommendations
require the demonstration of sensible risk management practices. Complying with this, can greatly improve your chances of avoiding criminal prosecution.
Typically, plant requiring inspection would include: Lifting equipment, Pressure systems, Boiler plant, LEV systems and general work equipment. This is not a comprehensive list. If in doubt contact the HSE or a qualified Engineer Surveyor.
For some new equipment, a manufacturer or supplier would typically have carried out a thorough examination which should be evidenced in a Declaration of Conformity. This is not guaranteed and advise should be taken from your supplier.
An Engineer Surveyor would be best placed to give advice on this. Frequencies could span from every month to every few years.